Success Story – Cutting problem in the polymer pelletizing industry
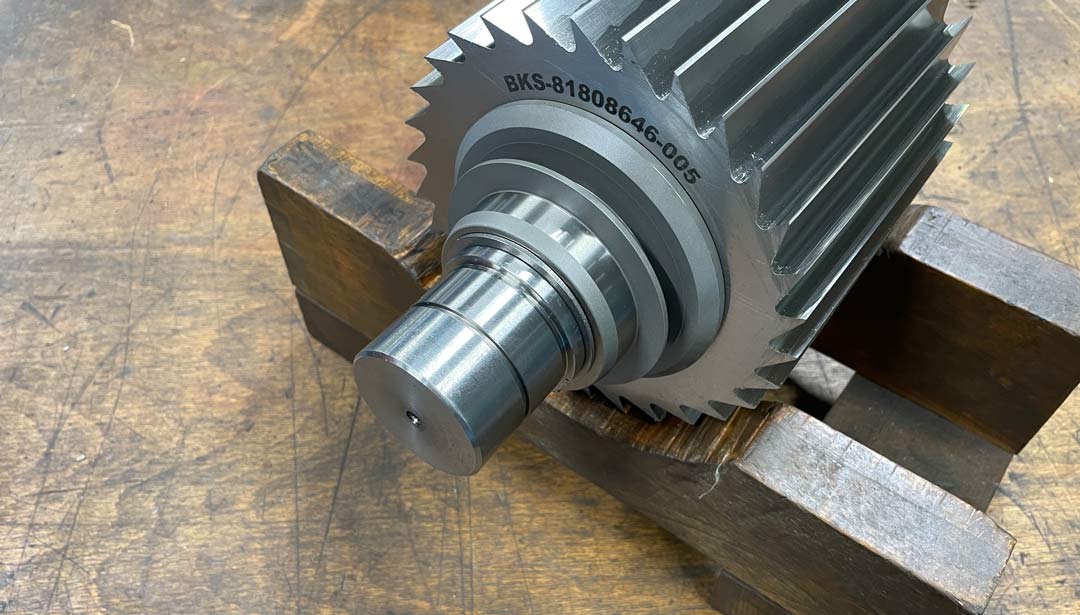
As Baptiste, one of our sales representatives, explained in the article BKS: your knives partner for Plastics Industry: the most important challenge for the pelletizing industry is to produce a plastic of impeccable and consistent quality.
Imperfect plastic pellets in the pelletizing industry
One of our customers had a cutting problem: his pellets were not cut cleanly. This meant that he could not satisfy his customers as he had hoped. Our customer didn’t know what the problem was. He sharpened the rotor very often to maximize the chances of a good result, but he didn’t completely solve his problem. He even considered investing in a new rotor with a different and expensive material.
Brainstorming, sharpening and production of a custom-made rotor
As we like to suggest to our customers and partners, we invited this customer to visit us in our Belgian workshop and organized a brainstorming session with the customer’s production team. During this brainstorming, we realized that our customer was working with TPU, a very flexible polymer. So, the problem was probably not the material of the rotor or its bluntness.
To be sure, we carried out a good regrinding made in BKS: the teeth and blades were sufficiently sharp for a good cut. But the result was still not conclusive. The real problem was, as we thought, the geometry of the teeth: their angles were not “aggressive” enough to cut our customer’s polymer properly.
We then offered our customer a custom-made rotor with a tooth geometry adapted to his needs. Indeed, at BKS, we produce new rotors and re-sharpen them entirely in-house. This allows us to produce all types of rotor geometries and materials and to fully satisfy our customers’ requirements.
As mentioned earlier, when brainstorming, we knew that TPU did not need a special rotor material. So, we simply produced a stainless-steel rotor, taking care to make the tooth geometry aggressive.
Results: many sources of savings!
The problem of cut quality is now solved. This solution has given our customer more reliability for his own customers, and fewer complaints. He has also made savings on the rotor, as stainless steel is much cheaper than a tungsten carbide rotor. Our customer also saves on production costs because the new rotor has a much longer running time and requires less resharpening.
Would you like to optimize the performance of your product or make savings? Contact us via this form and we will look for ways to improve together.