BKS develops a unique die plates wear resistant layer
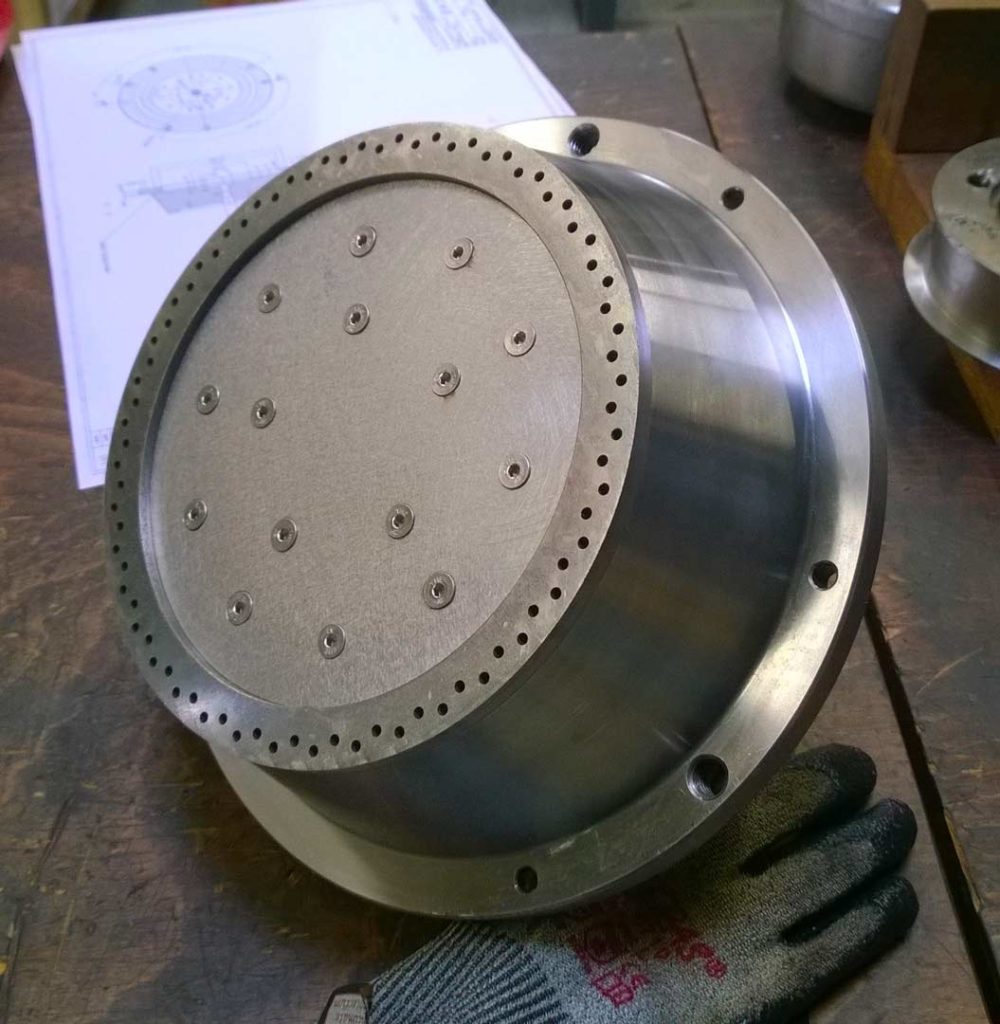
A new die plates technology
BKS has developed a new technology for the underwater pelletizing die plates from BKG/Nordson, Gala/Maag and many others. After several years of research and development, we have succeeded in developing a unique carbide layer applied by PTA welding for all our pelletizing dies.
Die plates are historically delivered with several carbide tiles that are brazed next to each other. The junction between the tiles is known to be a weak spot that may lead to damage in production.
Several advantages for the plastics industry
In contrast, our die plates made in BKS are made of a single continuous layer, not divided by segments. This layer, which is thicker than the OEM versions, is a combination of wear-resistant hard materials and a binder that distributes the tungsten carbide particles evenly. This has several advantages: a significantly longer service life (up to 2 times longer than OEM); minimal wear on the extrusion die face and therefore better pellet quality; no chipping unlike brazed tungsten carbide inserts which cause machine downtime; and finally, a cutting head that can be used down to the last 0.1 mm!
These recent developments allow our customers active in underwater plastic pelletizing (Compounding, Masterbatches, virgin materials, …) to increase their cutting quality while increasing their productivity.
Would you like an in-depth analysis of your needs? Contact us via this form and discover the solutions that our company can offer you.